Ponad 100 lat poświęconych postępowi technicznemu - tak najprościej można opisać naszą działalność w zakresie technologii robotycznej i automatyki Yaskawa.
Morat Swoboda: elastyczna automatyzacja w służbie elektromobilności
Yaskawa wspiera rozwój elektromobilności.
Dzięki innowacyjnej koncepcji automatyzacji produkcji firma Morat Swoboda Motion z impetem wkracza na rynek elektromobilności. Utworzone w 2018 r. przedsiębiorstwo uruchomiło niedawno w Nowej Rudzie nowoczesny zakład produkcyjny specjalizujący się w wytwarzaniu elementów elektrycznych układów napędowych.
Morat Swoboda Motion jest spółką joint venture utworzoną przez Franz Morat Group i dostawcę komponentów dla branży motoryzacyjnej – firmę Swoboda. Grupa Franz Morat od ponad 100 lat specjalizuje się w produkcji komponentów systemów napędowych – od kół zębatych po kompletne motoreduktory. Z kolei zatrudniająca 4200 pracowników firma Swoboda projektuje i wytwarza innowacyjne, wysoce precyzyjne komponenty i systemy dla sektora motoryzacyjnego, wyznaczając przyszłe kierunki rozwoju tego segmentu.
Tworząc joint venture, oba przedsiębiorstwa miały jeden nadrzędny cel: wejść na rynek elektromobilności. Zarówno Franz Morat Group, jak i Swoboda mają już spore doświadczenie w produkcji komponentów napędów elektrycznych. – Jednak nasze pierwsze wspólne zlecenie na dostawę elementów zębatych do silników rowerów elektrycznych – największe w historii Grupy Franz Morat – przerosło możliwości średniej wielkości przedsiębiorstwa. W tej sytuacji utworzenie joint venture okazało się najlepszym rozwiązaniem dla wszystkich zaangażowanych – zdradza kierownik projektu Stefan Mayer.
Partnerzy musieli sprostać wielu wyzwaniom: zbudować nową fabrykę, zaprojektować i wyposażyć linie produkcyjne oraz znaleźć i zatrudnić wykwalifikowany personel. A czasu na realizację ambitnego przedsięwzięcia mieli niewiele. – Od momentu przyjęcia zlecenia do położenia kamienia węgielnego pod nowy zakład w lipcu 2018 r. minęło dobre pół roku. W listopadzie do fabryki w Nowej Rudzie przyjechały pierwsze maszyny, a w marcu 2019 r. linie produkcyjne opuściły pierwsze, próbne partie produktów – wspomina Stefan Mayer.
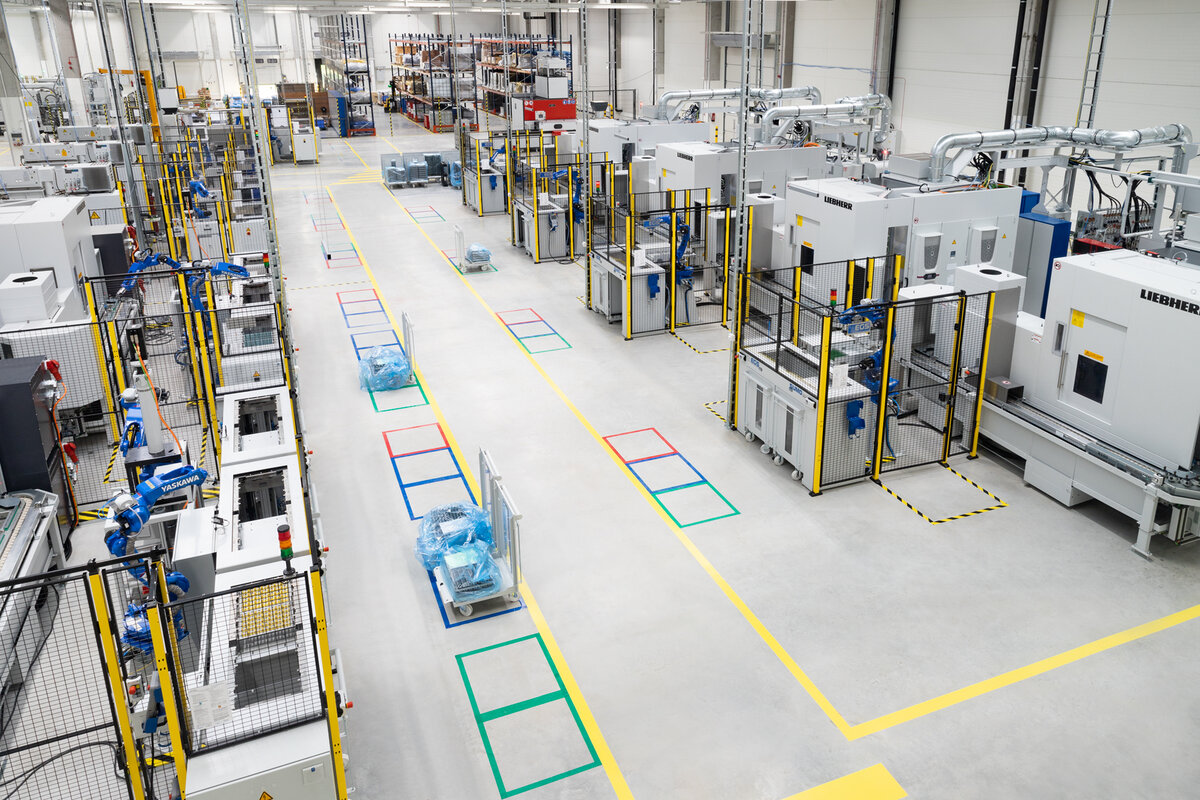
W poszukiwaniu złotego Graala
Szczególnie trudne okazało się opracowanie odpowiedniej strategii automatyzacji nowego zakładu. Obu partnerom zależało na tym, aby w elastyczny, inteligentny sposób połączyć cały park maszynowy w jeden ciąg technologiczny, a jednocześnie uzyskać taki stopień automatyzacji, który ograniczałby do minimum ingerencję człowieka. Wymagało to wyposażenia każdej maszyny we w pełni zautomatyzowany system załadunku i wyładunku.
Pierwsze pomysły zakładały wdrożenie wielu indywidualnych systemów pochodzących od różnych producentów. Tego typu rozwiązanie nie byłoby jednak w stanie spełnić wszystkich stawianych mu wymagań. Ostatecznie zdecydowano się na skorzystanie z koncepcji opracowanej przez niemiecką firmę EGS Automatisierungstechnik z Donaueschingen.
– Przekonało nas do niej to, że mogliśmy zrealizować wszystkie, nierzadko bardzo złożone zadania przy wykorzystaniu standardowych modułów dostarczonych przez EGS – wyjaśnia Stefan Mayer.
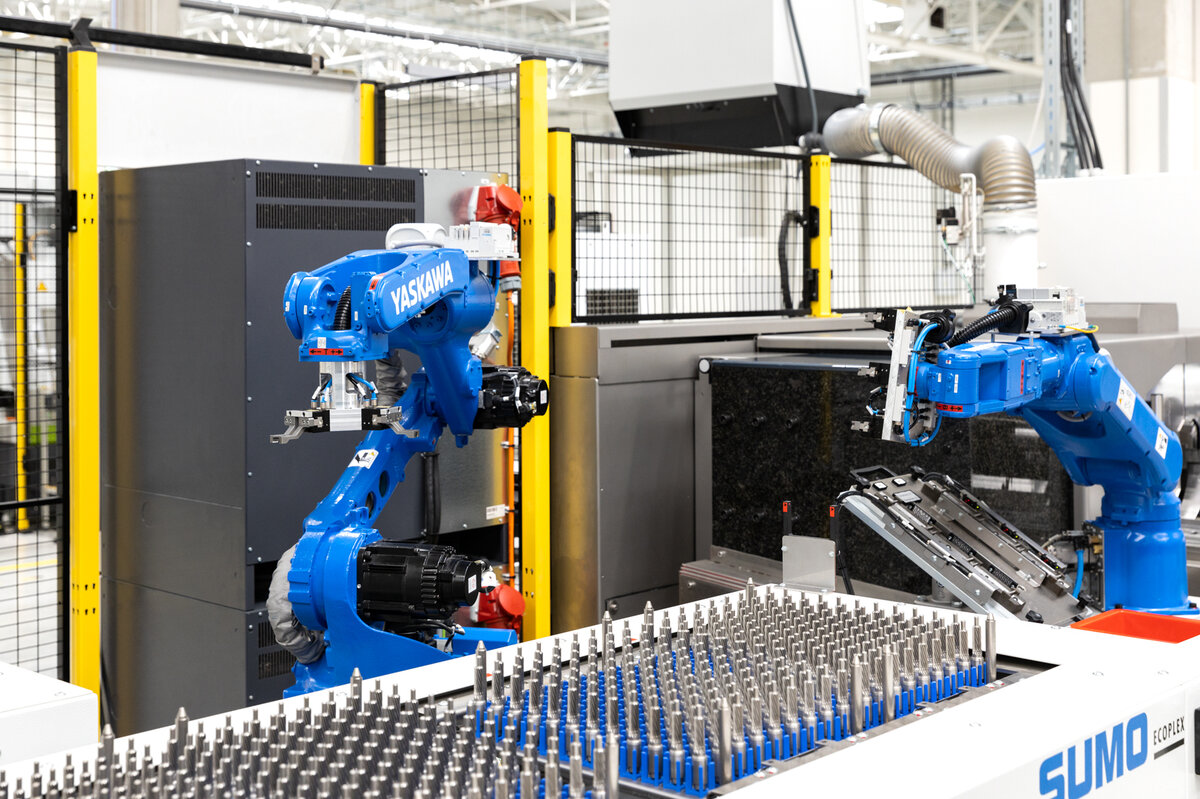
Tak proste, że aż genialne
Hartmut Pfalzgraf z zespołu handlowego firmy EGS dostrzegł od razu, że spełnienie wszystkich wymogów klienta wymaga zastosowania innowacyjnego, uniwersalnego rozwiązania. A takim bez wątpienia był system do paletyzacji SUMO Ecoplex2. – System składa się z dwóch wózków wsadowych do składowania części oraz robota Motoman firmy YASKAWA do przenoszenia detali oraz załadunku i wyładunku obrabiarki – wyjaśnia Hartmut Pfalzgraf. – Dzięki temu możemy jednocześnie zautomatyzować i zintegrować pracę maszyn, a dzięki możliwości ręcznego transportowania wózków zachowujemy wysoką elastyczność działania.
Aby w prosty sposób połączyć maszyny w jeden ciąg technologiczny, zastosowano identyczne palety systemowe, które można łatwo dostosować do wymiarów poszczególnych komponentów przez dopasowanie odpowiednich uchwytów i wkładek dystansowych. Po napełnieniu wszystkich półek pracownik pcha wózek na kolejne stanowisko obróbcze.
– System ten jest tyleż prosty, co genialny. Wytwarzane przez nas koła i wały przechodzą cały cykl produkcji bez konieczności sortowania czy jakiejkolwiek ingerencji pracowników. Zaś ręczny transport za pomocą wózków jest nie tylko najpewniejszą formą dostawy detali z punktu A do B, ale także zapewnia nam niezrównaną elastyczność działania – podkreśla Stefan Mayer.
Koncepcja ta ma jeszcze jedną decydującą zaletę: jeśli dana maszyna lub robot ulegnie awarii, nie powoduje to przestoju całej linii. Niewielkim nakładem pracy można produkować dalej, co zdecydowanie odróżnia ten system od konwencjonalnych, zintegrowanych „na sztywno” układów.
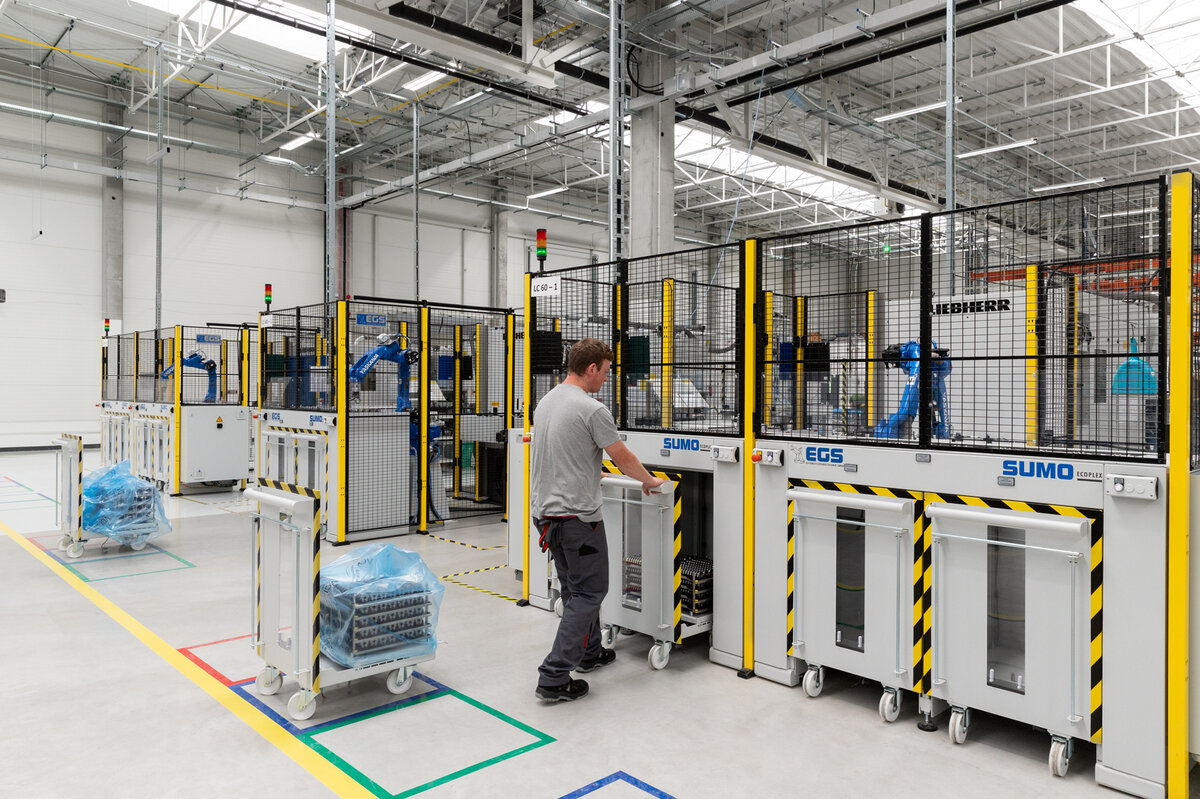
Roboty YASKAWA automatyzują pracę obrabiarek
Każda maszyna obróbcza wyposażona jest w co najmniej jeden system Ecoplex2 i robota YASKAWA. Firma EGS konsekwentnie postawiła na jeden konkretny typ robota – sprawdzony model Motoman MH12. Sześcioosiowa jednostka jest wprost stworzona do załadunku i wyładunku maszyn: jest szybka, precyzyjna, niezawodna i ma duży zasięg roboczy.
– Dzięki zasięgowi rzędu 1440 mm mogliśmy umiejscowić robota w relatywnie dużej odległości od obrabiarki, a tym samym zapewnić swobodny dostęp do maszyny. Dzięki temu operator może bez problemu przeprowadzić czynności serwisowe lub w razie potrzeby ręcznie załadować albo wyładować obrabiarkę – wyjaśnia Hartmut Pfalzgraf.
Tylko w jednym przypadku firma EGS musiała znaleźć MH12 godnego pomocnika. Rolę tę powierzyła mniejszemu, kompaktowemu robotowi MH5 LSII, który wsparł większego kuzyna w procesie załadunku i wyładunku jednej z obrabiarek o szczególnie krótkim czasie cyklu.
– Roboty YASKAWA od kilku lat pracują w naszej firmie Framo Morat i zdążyliśmy się już przekonać, że decyzja o ich zakupie była strzałem w dziesiątkę. Dlatego gdy przyszło do wyboru wyposażenia zakładu w Nowej Rudzie, znów postawiliśmy na produkty YASKAWY – wyjaśnia Stefan Mayer.
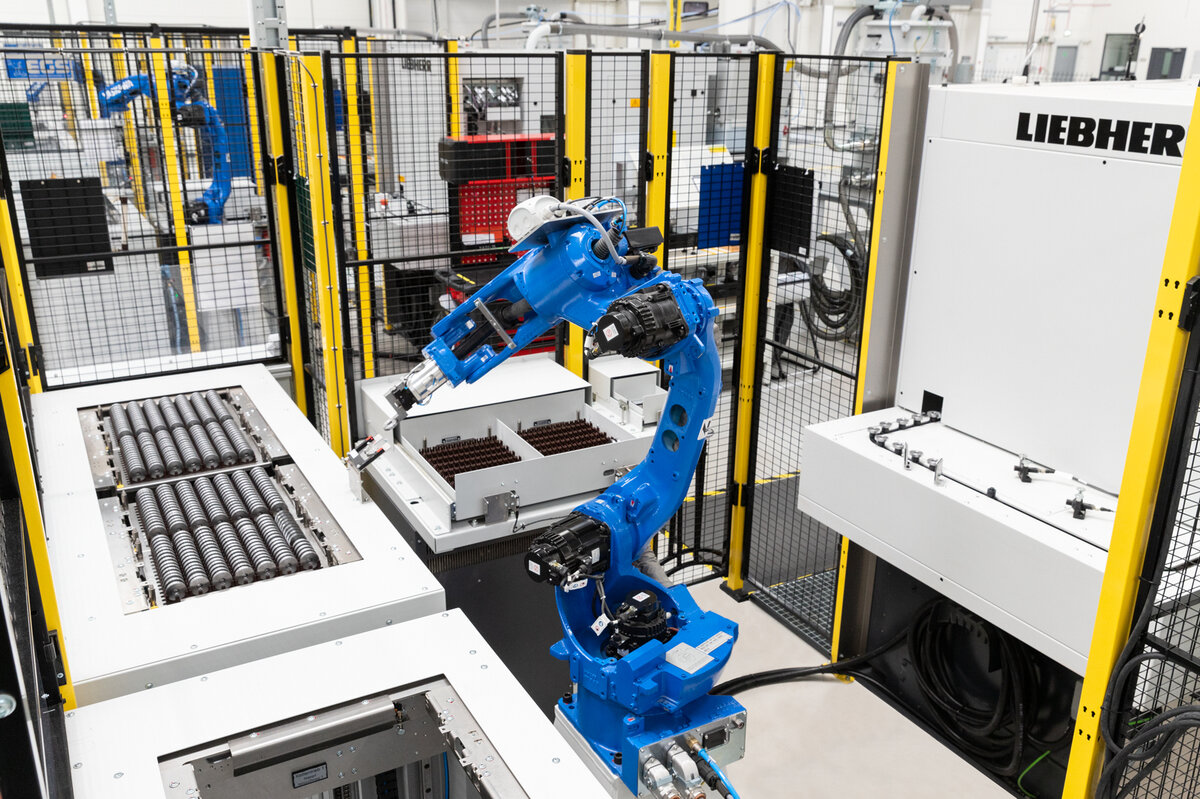
Szczupła produkcja w dosłownym znaczeniu tego słowa
Łącznie w produkcję komponentów napędów elektrycznych zaangażowanych jest 16 robotów YASKAWA i 20 systemów SUMO Ecoplex-2. Zaś za komunikację między obrabiarką a robotem odpowiada kontroler DX200 firmy YASKAWA. Jak się okazało, wysoki stopień automatyzacji i prosta obsługa systemu sprawiły, że inwestycja bardzo szybko się zwróciła.
Tym, co szczególnie istotne dla kierownictwa noworudzkiego zakładu, jest jakość finalnego wyrobu. Dlatego mimo wdrożenia nowoczesnego parku maszynowego i wysokiego poziomu automatyzacji zadań produkcyjnych nie zrezygnowano z przeprowadzania regularnej statystycznej kontroli procesu.
Dziś kierownik projektu Stefan Mayer patrzy na zakład w Nowej Rudzie z mieszaniną dumy i ulgi: – Rozruch fabryki przebiegł bez większych problemów. Wszystkie produkowane detale spełniają stawiane im wymogi, a jeśli popyt na komponenty rowerów elektrycznych będzie nadal wzrastał, możemy w prosty sposób rozbudować nasze linie produkcyjne, korzystając z gotowych, elastycznych modułów EGS.
Tekst: Ralf Högel, Tłumaczenie: Yaskawa, zdjęcia: Yaskawa
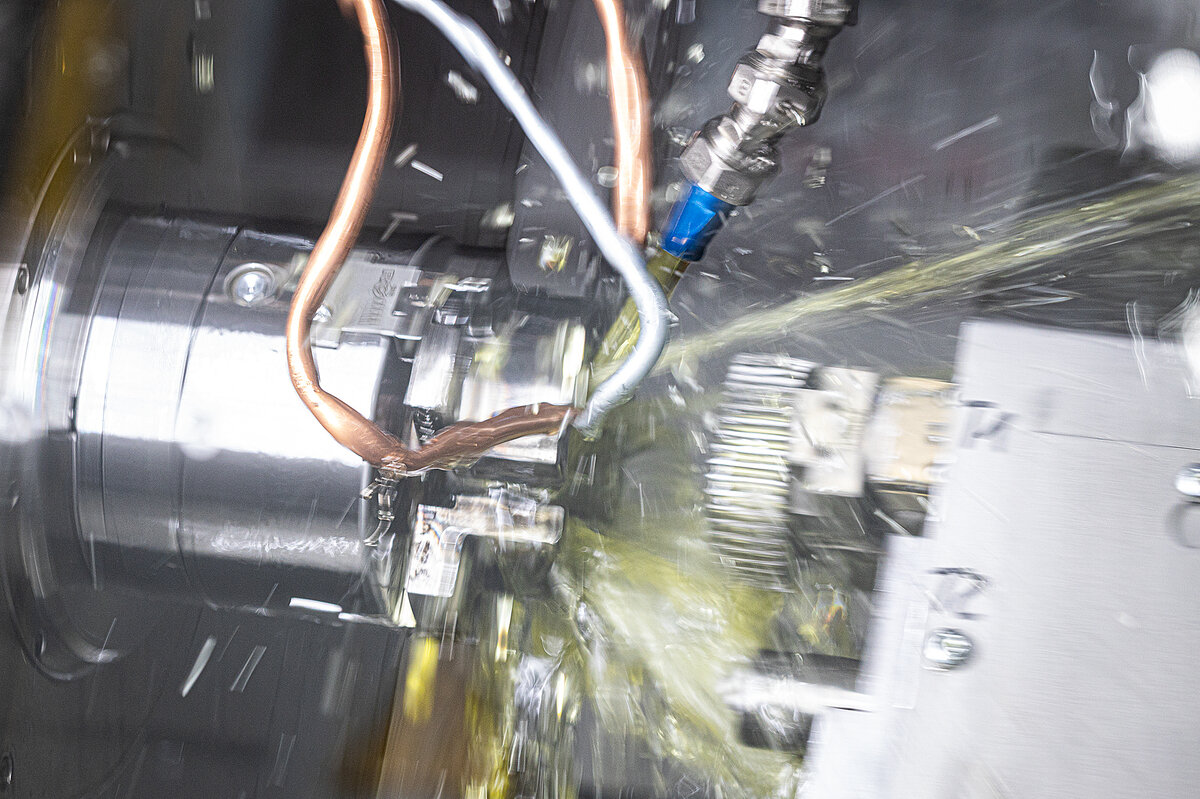