Ponad 100 lat poświęconych postępowi technicznemu - tak najprościej można opisać naszą działalność w zakresie technologii robotycznej i automatyki Yaskawa.
W pełni usystematyzowana produkcja piadin
Dzięki zastosowaniu kontrolera maszyn MP3300iec firmy Yaskawa włoskiemu integratorowi systemów Bosso Automazioni udało się zoptymalizować wydajność systemu Pick and Place zastosowanego u producenta tradycyjnych włoskich chlebków zwanych "piadina". Korzyści to niższe koszty eksploatacji, zapobieganie przestojom i odpadom, wydłużona żywotność urządzeń, a tym samym wyższa ogólna rentowność.
Historia piadin określanych przez włoskiego poetę Giovanniego Pascoli "narodowym chlebem Romanii" sięga czasów starożytnych Rzymian. Do dziś piadina jest uwielbiana zarówno przez młodych jak i starszych. Z biegiem lat ich produkcja przekroczyła granice Włoch i odnotowała gwałtowny wzrost na arenie międzynarodowej. Według danych Consortium for the Promotion and Protection of Piadina Romagnola w 2020 roku w wyniku pandemii Covid-19 produkcja piadin wzrosła jeszcze bardziej, osiągając imponujący poziom 22 030 ton. Odpowiada to wzrostowi o 23,3% w porównaniu z rokiem poprzednim. Zaspokojenie rosnącego popytu na rynku nie byłoby jednak możliwe bez dobrze funkcjonujących linii produkcyjnych.
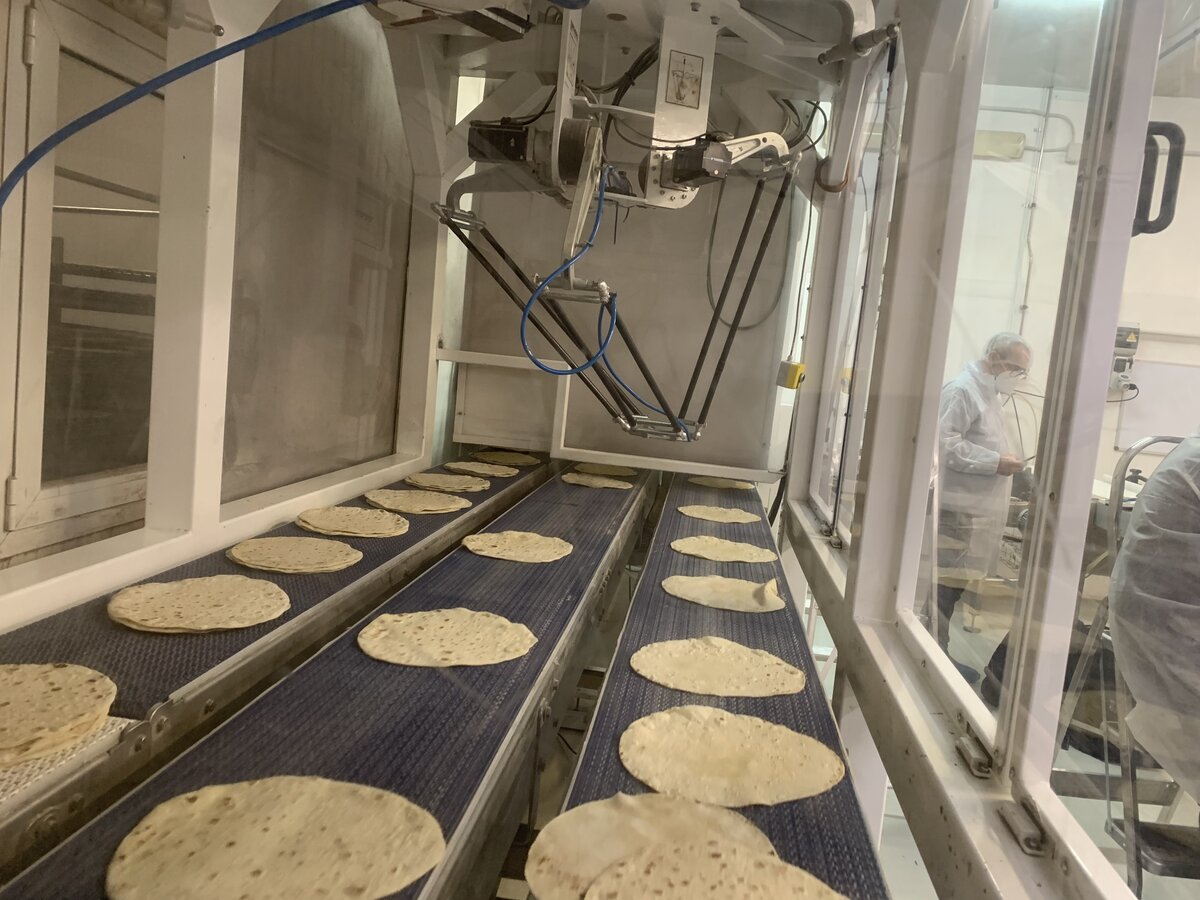
Niewystarczająco wydajny system Pick and Place
To właśnie niewystarczająco wydajny system był powodem, dla którego zakład produkujący piadiny w prowincji Rimini zwrócił się do integratora systemów Bosso Automazioni (www.bosso.it). Od 2001 roku integrator systemów z siedzibą w Rimini projektuje maszyny na zamówienie i współpracuje z firmą Yaskawa przy wdrażaniu jej innowacyjnych pomysłów.
Dzięki tej ścisłej współpracy firma mogła na nowo zaprojektować system Pick and Place w zakładzie, który jest wykorzystywany do układania piadin w stosy gotowe do pakowania. Poprzedni system był mocno przestarzały, oparty na starej koncepcji i zawierał elementy nie będące standardem przemysłowym (takie jak kamery).
Dzięki dwóm robotom delta, z których każdy był sterowany przez oddzielny kontroler z interfejsem MECHATROLINK-II i serwomotorami Sigma-7, linia produkcyjna nigdy nie osiągała pożądanych wyników. Pomimo dodania kolejnego robota, zakład wciąż borykał się z niską wydajnością, nieodpowiednimi uchwytami do mocowania produktów, częstymi awariami komponentów i przeciążeniem wzmacniaczy. Wzrost tempa produkcji wymagany dla zaspokojenia zapotrzebowania szczytowego sprawił, że problemy te tylko się pogłębiły.
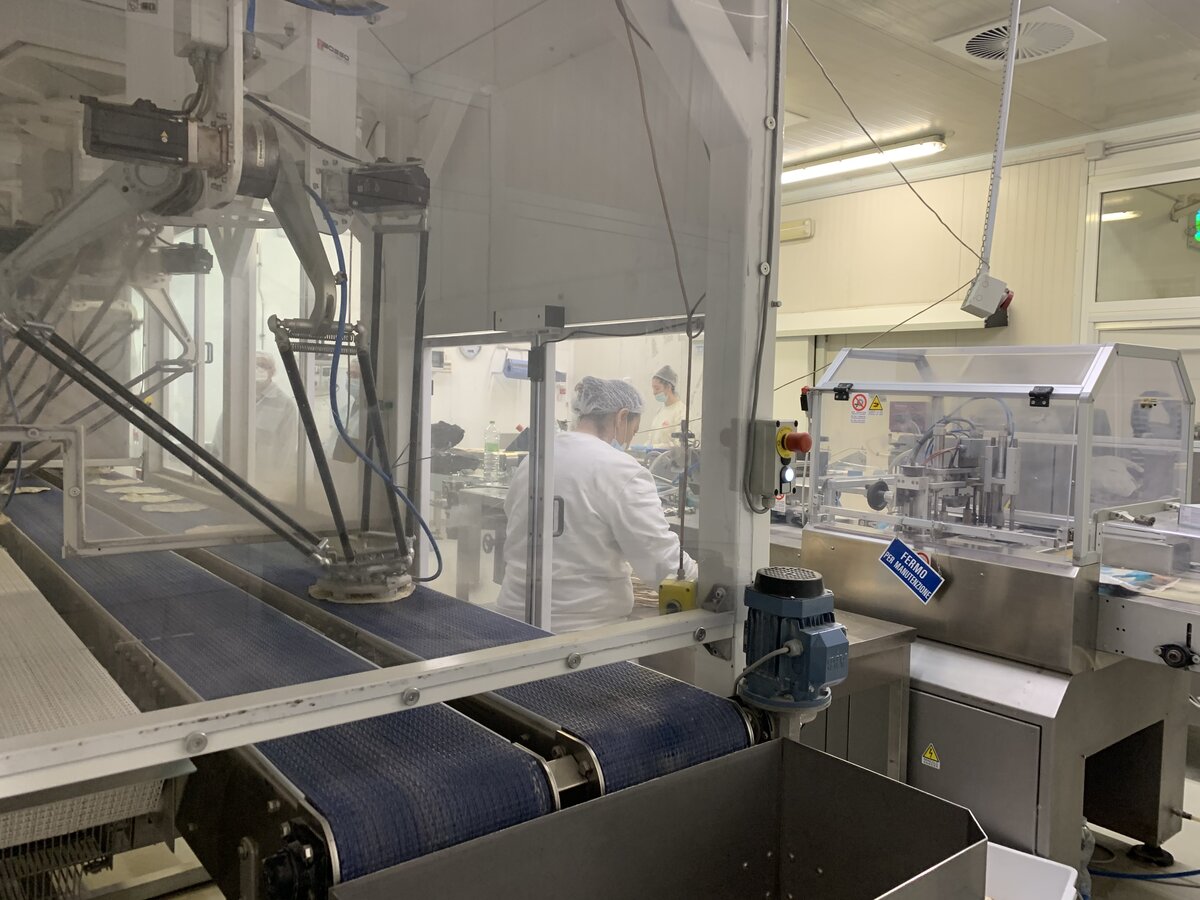
Złożone wymagania techniczne
Klient końcowy miał więc bardzo jasno sprecyzowane cele: wyeliminowanie problemów związanych z kontrolą, niezawodnością i cyklem, wzrost wydajności do 85 piadin na minutę (5100 piadin na godzinę), zmniejszenie ilości odpadów do mniej niż 3%, poprawa żywotności używanego sprzętu, usprawnienie kalibracji silnika i poprawa jakości sekwencji ruchów, aby zapobiec lub ograniczyć awarie serwomotorów. Dodatkowo zamierzano jak najbardziej zminimalizować liczbę zmian w istniejącym systemie.
Było to poważnie skomplikowane zadanie. Piadiny muszą być pobierane i odkładane pomiędzy poruszającymi się w przeciwnych kierunkach przenośnikami taśmowymi. Ponadto system wymaga dużej zmienności, zarówno w zakresie kształtu, jak i pozycjonowania. W związku z tym, aby pobierać i odkładać produkty, na ruchomych taśmach muszą być stosowane funkcje monitorowania przenośnika. Po długim procesie pieczenia piadiny wychodzą w nieregularnych odstępach czasu do dalszego studzenia. Klient miał jeszcze jedno wymaganie - opakowanie musi być tak zaprojektowane, aby pomieścić różną ilość produktów, a jednocześnie wyglądać estetycznie. Na górze opakowania musi być umieszczona piadina z tradycyjnymi ciemnymi śladami po pieczeniu, aby była pierwszą rzeczą, którą widzi klient.
Aby kontrolować cały proces, potrzebne było rozwiązanie, które mogłoby współdziałać z dużą liczbą komponentów (w tym niektórymi nieprzemysłowymi). Zdecydowano, że kontroler maszyn MP3300iec zostanie zintegrowany z oprogramowaniem sprzętowym mechanizmu sterowania. Przyjęto koncepcję wykorzystania jednego kontrolera dla całego systemu, co pozwoliło na lepszą kontrolę współdziałających funkcji komponentów.
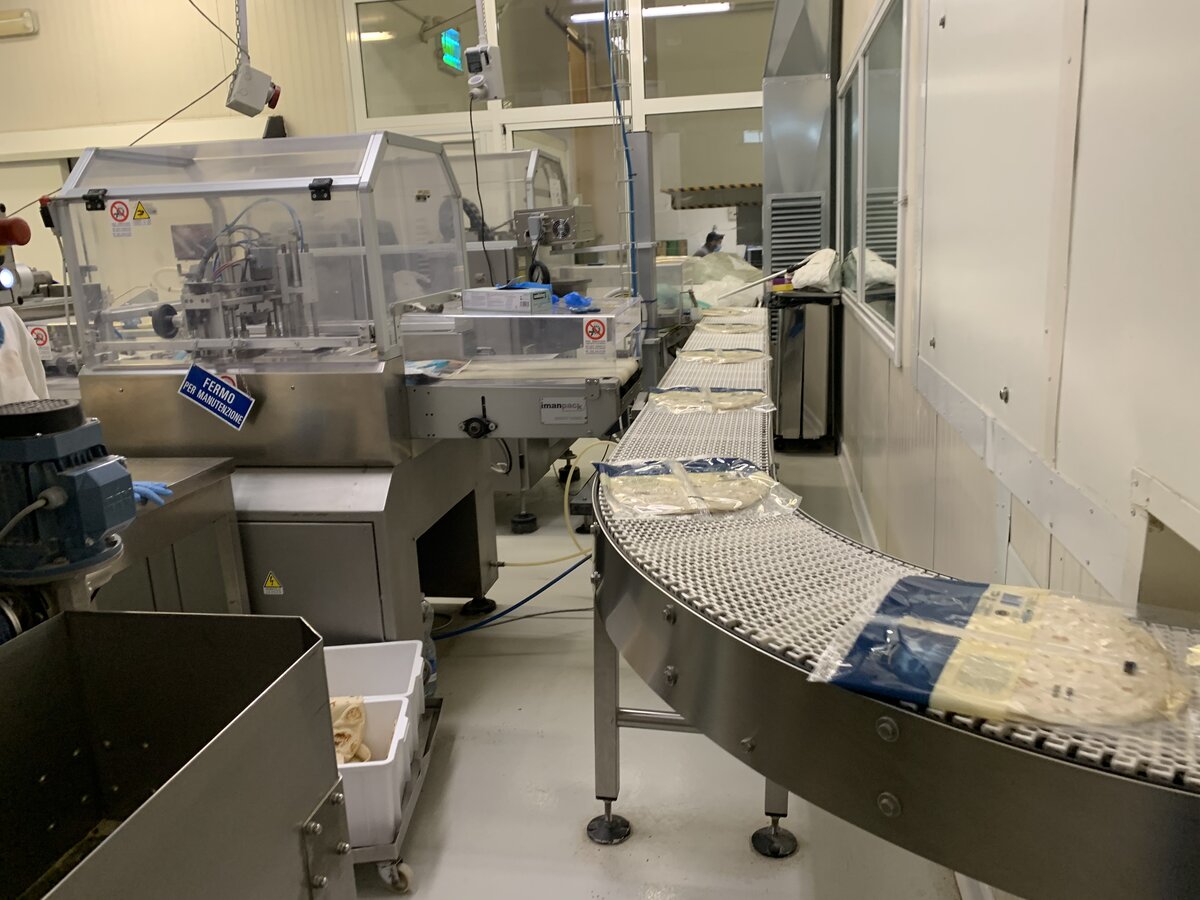
Symulacja podczas bieżącej produkcji
Był jednak jeszcze jeden czynnik powodujący komplikacje. Ponieważ użytkownik końcowy to dostawca supermarketów pracujący na trzy zmiany dziennie, migracja do w pełni zintegrowanego rozwiązania Yaskawa nie mogła przerwać produkcji.
Dynamika maszyny była dość złożona, zarówno ze względu na wysoki poziom zmienności, jak i zastosowanie kamery (zamiast konwencjonalnego systemu wizyjnego). Kamera umieszczona została poza obszarem roboczym robota, co jeszcze bardziej utrudniało kalibrację.
Ponadto system obejmował roboty innych firm. Po uwzględnieniu tych czynników wybrano kontroler maszyny MP3300iec RBT. Ponieważ nie było możliwości wcześniejszego przeprowadzenia próbnego uruchomienia, a produkcja nie mogła zostać zatrzymana, zespół firmy Yaskawa postanowił sprawdzić skuteczność algorytmów do sortowania w symulacji na panelu HMI celi.
Koncepcja zakładała opracowanie i przetestowanie aplikacji na symulatorze, a następnie przejście z symulacji na rzeczywistą maszynę. Wyniki były imponujące. Symulacja dopasowana do konkretnego zastosowania umożliwiła optymalizację zarządzania obciążeniem i szybką regulację prędkości robotów. Po uruchomieniu faktycznej celi symulator pozwalał na wizualizację procesu w czasie rzeczywistym. Elastyczne algorytmy opracowane na potrzeby aplikacji były również w stanie płynnie zarządzać specyficzną nierównomiernością produktów. Cel, jakim było układanie około 6 000 piadin na godzinę, został osiągnięty, a odsetek odpadów został zredukowany do zera.
Czynniki sukcesu i rezultaty
Wiedza firmy Yaskawa w zakresie gromadzenia danych, analizy ryzyka i zarządzania projektem była kluczem do sukcesu tego projektu. Nie bez znaczenia był również wynik w zakresie efektywności energetycznej: podczas gdy każdy robot Delta był pierwotnie sterowany przez osobny kontroler, aktualnie dla całego rozwiązania stosowany jest jeden kontroler. Obciążenie łączne zostało zredukowane do 55% wartości początkowej, a moc serwomotorów zmniejszono z 1,0 kW do 750 W.
Dzięki optymalizacji sekwencji ruchów udało się zwiększyć średnią żywotność urządzeń, obniżyć koszty operacyjne, zmniejszyć liczbę przestojów i odpadów, a tym samym uczynić zakład bardziej rentownym.